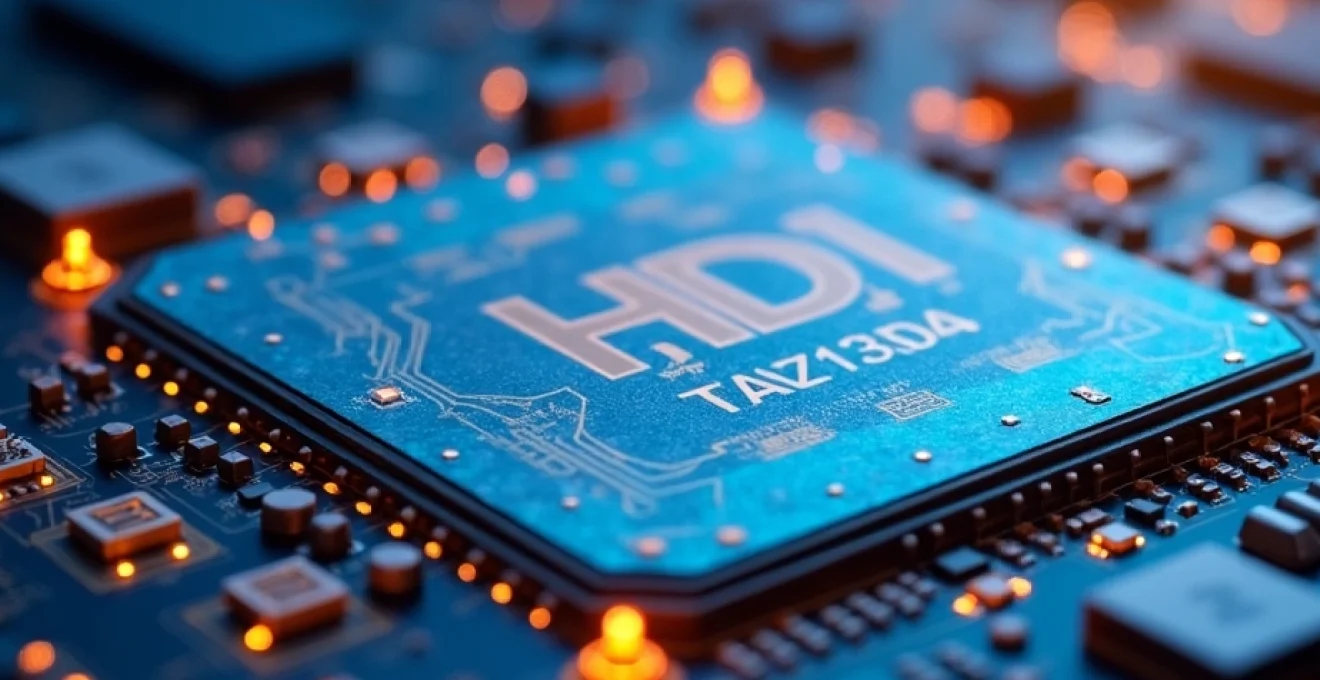
Die rasante Entwicklung der Elektronikbranche stellt ständig neue Anforderungen an Leiterplatten. High Density Interconnect (HDI) Leiterplatten repräsentieren den aktuellen Stand der Technik und ermöglichen immer kompaktere und leistungsfähigere elektronische Geräte. Durch ihre besonders hohe Packungsdichte und feine Strukturen bieten HDI-Leiterplatten entscheidende Vorteile gegenüber herkömmlichen Platinen. Sie sind der Schlüssel zur Miniaturisierung und Leistungssteigerung moderner Elektronik.
HDI-Technologie revolutioniert das Design von Smartphones, Wearables, medizinischen Geräten und vielen weiteren Anwendungen. Doch was genau macht diese Leiterplatten so besonders? Welche Herausforderungen müssen Entwickler und Hersteller bei der Umsetzung meistern? Und wie wird sich die HDI-Technologie in Zukunft weiterentwickeln? Dieser Artikel beleuchtet die wichtigsten Aspekte von HDI-Leiterplatten und gibt einen umfassenden Überblick über diese zukunftsweisende Technologie .
HDI-Leiterplatten für High-End-Elektronikanwendungen
HDI-Leiterplatten zeichnen sich durch eine außergewöhnlich hohe Packungsdichte aus. Im Vergleich zu herkömmlichen Leiterplatten ermöglichen sie die Integration von deutlich mehr Komponenten und Leiterbahnen auf der gleichen Fläche. Dies wird durch den Einsatz von Microvias, extrem feinen Leiterbahnen und mehreren Verdrahtungsebenen erreicht. Erfahren Sie mehr, indem Sie hier klicken und entdecken Sie die Vorteile dieser Technologie im Detail.
Ein wichtiges Merkmal von HDI-Leiterplatten sind die sogenannten Microvias. Diese winzigen Durchkontaktierungen mit einem Durchmesser von oft unter 100 μm ermöglichen die Verbindung zwischen den verschiedenen Lagen der Leiterplatte. Durch ihren geringen Platzbedarf können deutlich mehr Verbindungen realisiert werden als mit konventionellen Durchkontaktierungen. Gleichzeitig bieten Microvias exzellente elektrische Eigenschaften und tragen zur Verbesserung der Signalintegrität bei.
Die Leiterplatten-Industrie hat in den letzten Jahren enorme Fortschritte bei der Miniaturisierung gemacht. Aktuelle HDI-Designs erreichen Leiterbahnbreiten und -abstände von nur 50 μm oder weniger. Zum Vergleich: Ein menschliches Haar hat einen Durchmesser von etwa 100 μm. Diese extrem feinen Strukturen ermöglichen eine sehr effiziente Nutzung der verfügbaren Fläche.
HDI-Technologie hat die Grenzen des Machbaren in der Elektronik verschoben und eröffnet völlig neue Möglichkeiten für kompakte und leistungsfähige Geräte.
Durch die Kombination von Microvias und feinsten Leiterbahnen können HDI-Leiterplatten eine Anschlussdichte von über 500 Pins pro Quadratzentimeter erreichen. Dies macht sie zur idealen Plattform für moderne Hochleistungs-ICs mit extrem hoher Pinzahl. Gleichzeitig ermöglicht die hohe Packungsdichte eine Reduzierung der Gesamtgröße elektronischer Geräte bei gleicher oder sogar höherer Funktionalität.
Designüberlegungen bei der Entwicklung von HDI-Leiterplatten
Die Entwicklung von HDI-Leiterplatten stellt hohe Anforderungen an Designer und Ingenieure. Um das volle Potenzial dieser Technologie auszuschöpfen, müssen zahlreiche Faktoren berücksichtigt werden. Eine sorgfältige Planung des Lagenaufbaus, der Via-Strukturen und der Leiterbahngeometrie ist entscheidend für die Leistungsfähigkeit und Zuverlässigkeit des Endprodukts.
Lagenaufbau und Dicke der Leiterplatte
Der Lagenaufbau einer HDI-Leiterplatte hat großen Einfluss auf deren elektrische und mechanische Eigenschaften. Typischerweise werden mehrere Signallagen mit dedizierten Stromversorgungs- und Masselagen kombiniert. Die Anzahl und Anordnung der Lagen muss sorgfältig geplant werden, um optimale Signalintegrität und EMV-Eigenschaften zu erreichen.
Ein wichtiger Trend ist die Reduzierung der Gesamtdicke von HDI-Leiterplatten. Durch den Einsatz dünnerer Basismaterialien und Kupferfolien können Plattendicken von unter 0,6 mm realisiert werden. Dies ermöglicht den Einsatz in ultraflachen Geräten wie Smartphones oder Wearables. Allerdings stellt die geringe Dicke auch neue Herausforderungen an die mechanische Stabilität und das thermische Management.
Via-Strukturen und Microvias
Die effiziente Nutzung von Microvias ist ein Schlüsselfaktor für erfolgreiche HDI-Designs. Je nach Anforderung kommen verschiedene Via-Strukturen zum Einsatz:
- Blind Vias: Verbinden eine Außenlage mit einer inneren Lage
- Buried Vias: Verbinden ausschließlich innere Lagen
- Stacked Vias: Mehrere übereinander gestapelte Microvias
- Staggered Vias: Versetzt angeordnete Microvias für höhere Zuverlässigkeit
Die Wahl der optimalen Via-Struktur hängt von Faktoren wie der erforderlichen Verbindungsdichte, thermischen Belastung und Kosteneffizienz ab. Moderne HDI-Designs kombinieren oft verschiedene Via-Typen, um die Vorteile jeder Variante optimal zu nutzen.
Leiterbahnbreiten und Abstände
Die Miniaturisierung von Leiterbahnbreiten und -abständen ist ein wesentlicher Aspekt der HDI-Technologie. Aktuelle High-End-Designs erreichen Strukturbreiten von 50 μm oder weniger. Dies ermöglicht eine extrem hohe Routingdichte, stellt aber auch neue Anforderungen an die Fertigungsprozesse.
Bei der Festlegung von Leiterbahnbreiten müssen Faktoren wie Stromtragfähigkeit, Impedanz und Fertigungstoleranzen berücksichtigt werden. Besonders kritisch ist die Einhaltung definierter Impedanzen bei Hochgeschwindigkeitssignalen. Hier kommen oft spezielle Leiterbahngeometrien wie Coplanar Waveguides zum Einsatz.
Die Minimierung von Leiterbahnabständen erfordert eine sorgfältige Analyse möglicher Kopplungseffekte zwischen benachbarten Signalen. EMV-Aspekte und die Vermeidung von Übersprechen spielen eine wichtige Rolle bei der Optimierung des Layouts.
Fortschrittliche Fertigungstechnologien für HDI-Leiterplatten
Die Herstellung von HDI-Leiterplatten erfordert hochpräzise und innovative Fertigungstechnologien. Nur durch den Einsatz modernster Anlagen und Prozesse können die extrem feinen Strukturen zuverlässig und mit hoher Ausbeute produziert werden. Drei Schlüsseltechnologien sind besonders relevant für die HDI-Fertigung:
Laserbohrung von Microvias
Die Erzeugung von Microvias mit Durchmessern unter 100 μm stellt höchste Anforderungen an die Präzision. Moderne CO2- und UV-Laser ermöglichen die kontrollierte Ablation des Dielektrikums mit minimaler thermischer Belastung des umliegenden Materials. Durch präzise Steuerung von Pulsenergie und -dauer können selbst in dünnen Materialien saubere und zuverlässige Microvias erzeugt werden.
Ein entscheidender Vorteil der Laserbohrung ist die hohe Flexibilität. Anders als bei mechanischen Bohrverfahren können Microvias beliebig auf der Leiterplatte platziert werden. Dies ermöglicht eine optimale Ausnutzung des verfügbaren Platzes und unterstützt die Realisierung komplexer Via-Strukturen.
Oberflächenveredelung und Lötstopplack
Die extrem feinen Strukturen von HDI-Leiterplatten erfordern spezielle Oberflächenbehandlungen. Gängige Verfahren wie ENIG (Electroless Nickel Immersion Gold) oder OSP (Organic Solderability Preservative) müssen für HDI-Anwendungen optimiert werden. Besonders wichtig ist eine gleichmäßige Beschichtung auch in Microvias und unter feinsten SMD-Pads.
Beim Auftrag des Lötstopplacks kommen oft fotolithografische Verfahren zum Einsatz, um die erforderliche Präzision zu erreichen. Die exakte Platzierung der Lötstoppmaske ist entscheidend, um Kurzschlüsse zu vermeiden und gleichzeitig eine zuverlässige Benetzung der Lötflächen sicherzustellen.
Automatisierte optische Inspektion (AOI)
Die Qualitätskontrolle von HDI-Leiterplatten stellt höchste Anforderungen an die Inspektionssysteme. Moderne AOI-Anlagen nutzen hochauflösende Kameras und fortschrittliche Bildverarbeitungsalgorithmen, um selbst kleinste Defekte zuverlässig zu erkennen. Typische Prüfmerkmale umfassen:
- Leiterbahnbreiten und -abstände
- Kupferüberstände an Pads und Vias
- Qualität der Durchkontaktierungen
- Positionierung und Öffnungen im Lötstopplack
- Oberflächendefekte wie Kratzer oder Verunreinigungen
Die automatisierte Inspektion ermöglicht eine 100%-Prüfung aller produzierten Leiterplatten und trägt so entscheidend zur Qualitätssicherung bei. Gleichzeitig liefern die gewonnenen Daten wertvolle Informationen zur kontinuierlichen Optimierung der Fertigungsprozesse.
Die Kombination aus hochpräzisen Fertigungsverfahren und lückenloser Qualitätskontrolle ist der Schlüssel zur zuverlässigen Produktion von HDI-Leiterplatten.
Zuverlässigkeitstests für HDI-Leiterplatten
Die hohe Packungsdichte und feinen Strukturen von HDI-Leiterplatten stellen besondere Anforderungen an die Zuverlässigkeit. Um die Langzeitstabilität unter realen Einsatzbedingungen sicherzustellen, werden umfangreiche Tests durchgeführt. Diese simulieren typische Belastungen wie thermische Zyklen, mechanische Vibrationen oder Feuchtigkeitseinflüsse.
Ein kritischer Aspekt ist die Zuverlässigkeit der Microvias. Aufgrund ihrer geringen Größe sind diese besonders anfällig für thermomechanische Belastungen. Standardisierte Tests wie der IST (Interconnect Stress Test) oder Thermal Cycling dienen zur Bewertung der Via-Zuverlässigkeit. Dabei werden die Leiterplatten einer großen Zahl von Temperaturzyklen ausgesetzt, um potenzielle Schwachstellen zu identifizieren.
Die mechanische Stabilität wird durch Tests wie den Drop Test oder Vibration Test überprüft. Diese sind besonders relevant für mobile Geräte, die häufig Stößen und Erschütterungen ausgesetzt sind. Spezielle Aufmerksamkeit gilt dabei der Integrität von Lötverbindungen und der Haftung von Bauteilen auf der Leiterplatte.
Feuchtigkeitsbeständigkeit spielt eine wichtige Rolle für die Langzeitstabilität. Der 85/85 Test (85°C / 85% relative Luftfeuchtigkeit) simuliert extreme Umgebungsbedingungen und ermöglicht die Bewertung von Korrosionseffekten und Delaminationsrisiken. Besonders kritisch sind dabei die Grenzflächen zwischen verschiedenen Materialien wie Kupfer und Dielektrikum. Die folgende Tabelle enthält weitere Informationen:
Testverfahren | Simulierte Belastung | Typische Testparameter |
---|---|---|
Thermal Cycling | Temperaturwechsel | -55°C bis +125°C, 1000 Zyklen |
Drop Test | Mechanische Stöße | 1,5 m Fallhöhe, 6 Aufschlagpositionen |
85/85 Test | Feuchtigkeit/Temperatur | 85°C, 85% RH, 1000 Stunden |
Die Ergebnisse dieser Zuverlässigkeitstests fließen direkt in die Optimierung von Designregeln und Fertigungsprozessen ein. Nur durch kontinuierliche Verbesserung kann die hohe Qualität und Zuverlässigkeit von HDI-Leiterplatten auch bei steigenden Anforderungen sichergestellt werden.
Zukunftsperspektiven für HDI-Leiterplattentechnologie
Die rasante Entwicklung der Elektronikbranche treibt die Nachfrage nach immer kompakteren und leistungsfähigeren elektronischen Geräten. HDI-Leiterplatten werden auch in Zukunft eine Schlüsselrolle bei der Realisierung innovativer Produkte spielen. Einige wichtige Trends und Entwicklungen zeichnen sich bereits ab:
Die Miniaturisierung schreitet weiter voran. Experten erwarten, dass Leiterbahnbreiten und -abstände von unter 30 μm in naher Zukunft zum Standard werden. Dies erfordert weitere Fortschritte in der Fertigungstechnologie, insbesondere bei Lithografie und Ätztechniken. Gleichzeitig müssen neue Materialien entwickelt werden, die den steigenden Anforderungen an Signalintegrität und thermische Stabilität gerecht werden.
Ein vielversprechender Ansatz ist die Integration von aktiven und passiven Komponenten direkt in die Leiterplatte. Durch das Einbetten von Widerständen, Kondensatoren oder sogar ICs lässt sich die Packungsdichte nochmals erhöhen. Gleichzeitig verbessern sich die elektrischen Eigenschaften durch kürzere Verbindungswege. Allerdings stellt diese Technologie neue Herausforderungen an Entwurf, Fertigung und Reparierbarkeit.
Die nächste Generation von HDI-Leiterplatten wird die Grenzen zwischen Leiterplatte und Bauelementen zunehmend verwischen.
Flexible und dehnbare Elektronik eröffnet völlig neue Anwendungsfelder für HDI-Technologie. Durch den Einsatz flexibler Substrate und spezieller Leiterstrukturen können elektronische Schaltungen in Textilien, medizinische Implantate oder adaptive Oberflächen integriert werden. Dies erfordert jedoch neuartige Materialien und Fertigungsverfahren, die extreme mechanische Belastungen zuverlassen.
Die zunehmende Verbreitung von 5G und anderen Hochfrequenzanwendungen stellt besondere Anforderungen an HDI-Leiterplatten. Spezielle HF-taugliche Materialien und Designtechniken wie eingebettete Wellenleiter werden an Bedeutung gewinnen. Gleichzeitig müssen Aspekte wie Signalintegrität und elektromagnetische Verträglichkeit noch stärker berücksichtigt werden.
Nachhaltigkeit und Umweltverträglichkeit rücken auch bei HDI-Leiterplatten in den Fokus. Die Entwicklung bleifreier Prozesse und recyclingfähiger Materialien wird vorangetrieben. Gleichzeitig arbeiten Forscher an Methoden zur Wiederverwendung und Aufbereitung von HDI-Leiterplatten, um den Ressourcenverbrauch zu reduzieren.
Die fortschreitende Digitalisierung und künstliche Intelligenz werden auch die Entwicklung von HDI-Leiterplatten beeinflussen. KI-gestützte Designtools ermöglichen die automatisierte Optimierung komplexer Layouts. In der Fertigung kommen verstärkt intelligente Prozesssteuerungen zum Einsatz, die eine adaptive Anpassung der Produktionsparameter erlauben.