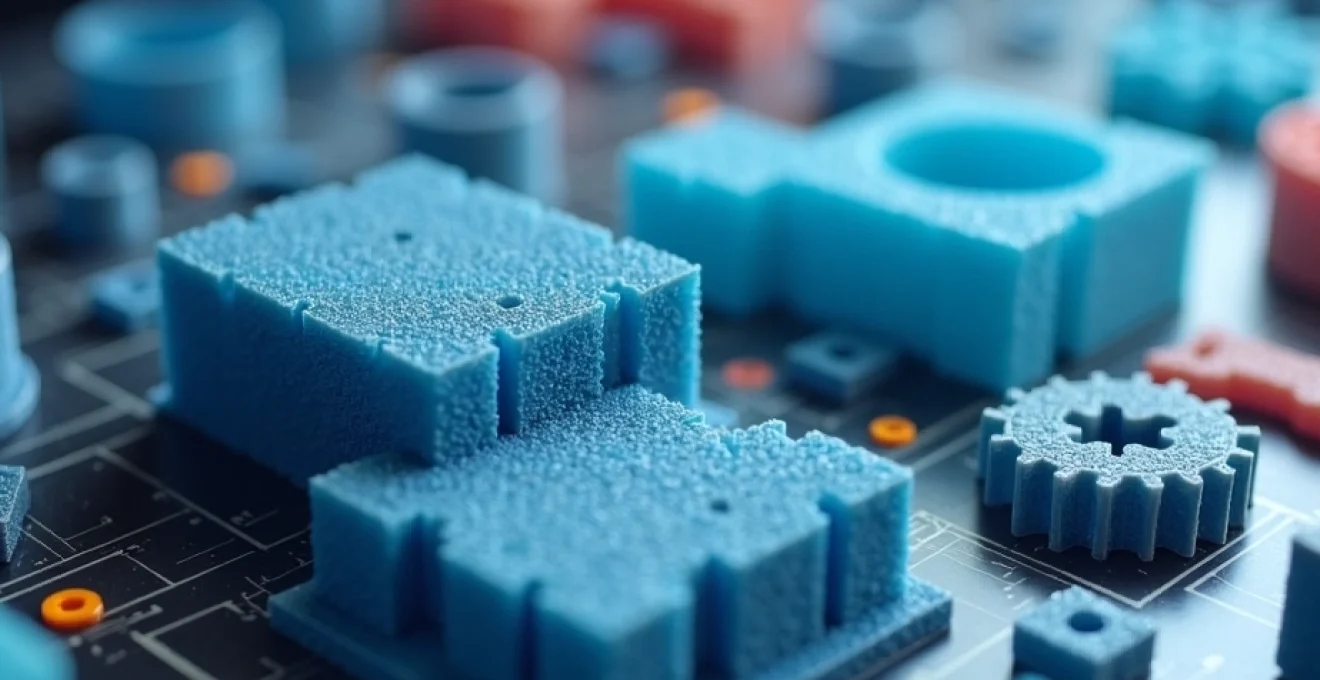
Der 3D-Druck hat sich von einer Nischentechnologie zu einem tragenden Element der industriellen Fertigung entwickelt. Was vor wenigen Jahrzehnten noch als experimentelles Verfahren galt, transformiert heute fundamentale Produktionsprozesse in nahezu allen Industriebereichen. Mit der Fähigkeit, hochkomplexe Geometrien direkt aus digitalen Modellen zu erzeugen, überwindet die additive Fertigung bisherige Grenzen der konventionellen Produktion. Besonders in Deutschland haben Unternehmen wie Siemens, BMW und Airbus diese Technologie strategisch in ihre Fertigungsabläufe integriert und erzielen damit erhebliche Effizienzgewinne, Materialeinsparungen und völlig neue Produktfunktionalitäten.
Die Bedeutung des 3D-Drucks steigt parallel zur fortschreitenden Digitalisierung der Industrie 4.0, da sich durch diese Technologie Materialien präziser, ressourcenschonender und mit deutlich reduzierten Vorlaufzeiten verarbeiten lassen. Aktuelle Marktanalysen prognostizieren für den industriellen 3D-Druck ein jährliches Wachstum von über 20 Prozent in den kommenden fünf Jahren. Diese rasante Entwicklung wird insbesondere durch Fortschritte bei Druckgeschwindigkeiten, Materialvielfalt und nahtloser Produktionsintegration vorangetrieben.
Grundlagen der additiven Fertigungstechnologien in der Industrie 4.0
Die additive Fertigung repräsentiert einen fundamentalen Paradigmenwechsel in der industriellen Produktion. Im Gegensatz zu subtraktiven Verfahren wie Fräsen oder Drehen, bei denen Material abgetragen wird, baut der 3D-Druck Objekte schichtweise auf. Dieser grundlegende Unterschied ermöglicht völlig neue Konstruktions- und Fertigungsansätze, die mit konventionellen Methoden entweder unmöglich oder wirtschaftlich nicht darstellbar wären. Die strukturelle Integration in Industrie 4.0-Umgebungen erfolgt dabei über durchgängige digitale Prozessketten, die vom CAD-Modell bis zur fertigen Komponente reichen.
Der industrielle 3D-Druck basiert auf dem Prinzip der schrittweisen Materialanlagerung, wobei verschiedene physikalische oder chemische Prozesse zum Einsatz kommen, um die einzelnen Schichten zu verbinden. Die Verarbeitungsgeschwindigkeit hat sich in den letzten fünf Jahren drastisch erhöht – moderne Anlagen erreichen mittlerweile Baugeschwindigkeiten von bis zu 100 cm³ pro Stunde bei Metallteilen, was selbst für mittlere Serienproduktionen wirtschaftlich interessant wird.
Ein entscheidender Vorteil der additiven Fertigung liegt in der Designfreiheit. Während herkömmliche Herstellungsverfahren durch Werkzeugzugänglichkeit und Fertigungsbeschränkungen limitiert sind, erlaubt der 3D-Druck beinahe unbegrenzte geometrische Komplexität ohne zusätzliche Kosten. Dies eröffnet völlig neue Möglichkeiten für Leichtbaustrukturen, funktionale Integration und topologieoptimierte Bauteile, die genau dort Material einsetzen, wo es strukturell benötigt wird.
Für die Einbettung in Industrie 4.0-Umgebungen bietet die additive Fertigung ideale Voraussetzungen, da sie von Grund auf digital ist. Vom CAD-Modell über die Schichtdatengenerierung bis hin zur Maschinensteuerung sind alle Prozessschritte durchgängig digital, was eine nahtlose Integration in vernetzte Produktionssysteme ermöglicht. Diese digitale Durchgängigkeit bildet die Grundlage für flexible Fertigungskonzepte, die eine bedarfsorientierte Produktion ohne umfangreiche Werkzeugvorbereitungen ermöglichen.
Die additive Fertigung verändert nicht nur, wie wir produzieren, sondern grundlegend, was wir überhaupt produzieren können. Sie beseitigt Konstruktionsbeschränkungen, die seit Jahrhunderten als unüberwindbar galten.
Besonders relevant ist auch die Verknüpfung mit anderen digitalen Technologien: Künstliche Intelligenz optimiert Bauteile automatisch für den 3D-Druck, während digitale Zwillinge virtuelle Tests ermöglichen, bevor das erste physische Teil gedruckt wird. In Deutschland haben mittlerweile über 37% der produzierenden Unternehmen 3D-Drucktechnologien in ihre Prozesse integriert, wobei die Anwendungsbereiche von Prototypenbau über Werkzeugherstellung bis zur direkten Serienproduktion reichen.
Aktuelle 3D-Druck-Verfahren im industriellen Kontext
Die Vielfalt der industriellen 3D-Druckverfahren hat sich in den letzten Jahren erheblich erweitert, wobei jede Technologie spezifische Stärken für bestimmte Anwendungsszenarien bietet. Die Wahl des optimalen Verfahrens hängt maßgeblich von Faktoren wie Materialanforderungen, Geometriekomplexität, Produktionsvolumen und Qualitätsansprüchen ab. Für die industrielle Fertigung haben sich fünf Hauptverfahren etabliert, die jeweils unterschiedliche Nischen besetzen.
Die verschiedenen Technologien unterscheiden sich fundamental in ihren physikalischen Wirkprinzipien: Während einige Verfahren mit Lasern arbeiten, nutzen andere Extrusionsprozesse oder photochemische Reaktionen. Diese Vielfalt ermöglicht es, für nahezu jede Anwendung die passende Technologie auszuwählen – vom hochpräzisen Mikrodesign bis zum großvolumigen Industriebauteil mit mehreren Metern Ausdehnung.
Selektives Lasersintern (SLS) bei BMW und Airbus
Das Selektive Lasersintern (SLS) hat sich als robustes Verfahren für die Serienfertigung funktionaler Bauteile etabliert. Bei diesem Prozess schmilzt ein Laser selektiv Pulvermaterial wie Polyamid, TPU oder spezielle Hochleistungskunststoffe schichtweise zusammen. BMW nutzt diese Technologie intensiv für die Herstellung komplexer Komponenten in der Fahrzeugproduktion, insbesondere für Teile mit integrierten Funktionen und Leichtbaustrukturen.
Ein herausragender Vorteil von SLS besteht darin, dass keine Stützstrukturen benötigt werden, da das nicht versinterte Pulver das Bauteil während des Druckprozesses stützt. Dies ermöglicht die Fertigung hochkomplexer Geometrien mit Hinterschneidungen und innenliegenden Strukturen. Bei BMW werden mittlerweile über 80.000 Kunststoffteile jährlich per SLS-Verfahren produziert, wobei sich die Durchlaufzeiten gegenüber konventionellen Fertigungsmethoden um bis zu 75% reduziert haben.
Airbus setzt SLS insbesondere für Leichtbaukomponenten im Flugzeugbau ein, wo jedes eingesparte Gramm über die gesamte Lebensdauer des Flugzeugs zu erheblichen Kraftstoffeinsparungen führt. Die Technologie ermöglicht die Integration von bis zu 20 Einzelkomponenten in ein einziges Bauteil, was neben Gewichtseinsparungen auch die Montagezeit drastisch reduziert und die Zuverlässigkeit durch weniger Verbindungsstellen erhöht.
Fused Deposition Modeling (FDM) in der Serienfertigung
Das Fused Deposition Modeling (FDM), auch als Fused Filament Fabrication (FFF) bekannt, hat sich vom einstigen Prototyping-Verfahren zu einer ernstzunehmenden Produktionstechnologie entwickelt. Bei diesem Verfahren wird thermoplastisches Filament durch eine beheizte Düse extrudiert und schichtweise aufgetragen. Die Technologie besticht durch ihre Kosteneffizienz und Skalierbarkeit, was sie besonders für mittelgroße Serien attraktiv macht.
Dank erheblicher Fortschritte bei Druckgeschwindigkeiten und Materialqualität setzen immer mehr Unternehmen auf FDM für die direkte Produktion von Endteilen. Die neueste Generation von Industrieanlagen erreicht Präzisionen von ±0,1 mm bei Baugeschwindigkeiten von bis zu 500 cm³ pro Stunde. Besonders in der Automotive-Zulieferindustrie nutzen Unternehmen diese Technologie für Kleinserien und kundenspezifische Komponenten.
Ein signifikanter Fortschritt liegt in der Entwicklung von Hochtemperatur-Druckkammern, die die Verarbeitung von technischen Kunststoffen wie PEEK, PEKK und ULTEM ermöglichen. Diese Materialien bieten hervorragende mechanische Eigenschaften und Temperaturbeständigkeit, was die Anwendung in anspruchsvollen industriellen Umgebungen erlaubt. Durch den Einsatz von kontinuierlicher Faserverstärkung während des Druckprozesses können zudem Bauteile hergestellt werden, die in ihren mechanischen Eigenschaften mit Aluminium konkurrieren können.
Stereolithografie (SLA) für Präzisionsteile bei Siemens
Die Stereolithografie (SLA) zeichnet sich durch ihre außergewöhnliche Oberflächenqualität und Detailgenauigkeit aus, was sie zum bevorzugten Verfahren für hochpräzise Komponenten macht. Bei diesem Prozess härtet ein UV-Laser flüssiges Photopolymer schichtweise aus. Siemens nutzt diese Technologie intensiv für die Fertigung komplexer Komponenten mit feinen Details und hohen Anforderungen an Maßhaltigkeit.
Moderne industrielle SLA-Systeme erreichen Schichtdicken von nur 25 Mikrometern und Baugenauigkeiten von bis zu ±0,05 mm, was sie ideal für Anwendungen in der Medizintechnik, Optik und Elektronik macht. Siemens Energy setzt SLA-Verfahren für die Produktion von Gasturbinenkomponenten ein, wobei die Technologie besonders für komplexe Kühlkanäle und Strömungsoptimierungen genutzt wird.
Ein wesentlicher Fortschritt liegt in der kontinuierlichen Weiterentwicklung der Photopolymere, die mittlerweile Eigenschaften bieten, die mit technischen Kunststoffen vergleichbar sind. Spezielle Harze mit Keramik- oder Metallpartikeln ermöglichen zudem den Druck von Komponenten, die anschließend gesintert werden können, um vollwertige keramische oder metallische Bauteile zu erhalten. Diese Hybridprozesse kombinieren die Formfreiheit des 3D-Drucks mit den Materialeigenschaften konventioneller Werkstoffe.
Direct Metal Laser Sintering (DMLS) in der Luft- und Raumfahrt
Das Direct Metal Laser Sintering (DMLS) hat die Metallverarbeitung revolutioniert, indem es die direkte Herstellung komplexer Metallbauteile ohne Umwege ermöglicht. Bei diesem Verfahren verschmilzt ein Hochleistungslaser selektiv Metallpulver, wodurch schichtweise ein solides Metallteil entsteht. Die Luft- und Raumfahrtindustrie hat diese Technologie früh adaptiert und treibt ihre Weiterentwicklung maßgeblich voran.
Führende Unternehmen wie MTU, Rolls-Royce und GE Aviation nutzen DMLS für kritische Komponenten in Triebwerken, wo topologieoptimierte Designs zu erheblichen Leistungssteigerungen führen. Ein Paradebeispiel ist die Brennkammerdüse des GE LEAP-Triebwerks, bei der 20 einzeln gefertigte Komponenten durch ein einziges 3D-gedrucktes Teil ersetzt wurden, was zu einer Gewichtsreduktion von 25% und einer fünffach längeren Lebensdauer führte.
Die jüngsten Entwicklungen im DMLS-Bereich konzentrieren sich auf Prozessstabilität und Qualitätssicherung, da für sicherheitskritische Anwendungen eine konstante Materialqualität unerlässlich ist. Moderne Anlagen verfügen über integrierte Überwachungssysteme, die jeden Schmelzvorgang in Echtzeit analysieren und Anomalien sofort erkennen. Diese In-Process-Monitoring -Systeme ermöglichen eine lückenlose Dokumentation und Rückverfolgbarkeit, was besonders für zertifizierte Bauteile in der Luftfahrt essentiell ist.
PolyJet und MultiJet Modeling für mehrfarbige Funktionsteile
Die PolyJet- und MultiJet-Modeling-Technologien (MJM) bieten einzigartige Möglichkeiten für mehrfarbige und multimaterielle Komponenten. Ähnlich wie bei Tintenstrahldruckern werden dabei mikroskopisch kleine Tröpfchen von Photopolymeren präzise platziert und durch UV-Licht ausgehärtet. Diese Verfahren ermöglichen die Kombination verschiedener Materialhartstufen und Farben in einem einzigen Druckvorgang.
Besonders in der Konsumgüterindustrie, bei Medizinprodukten und in der Produktentwicklung bieten diese Technologien enormes Potenzial. Sie ermöglichen die Herstellung von Bauteilen mit integrierten weichen und harten Komponenten, was traditionell nur durch komplexe Mehrkomponenten-Spritzgussverfahren möglich war. Die Materialauswahl reicht von gummiartigen Elastomeren mit Shore-Härten von 27A bis zu rigiden Kunststoffen, die ABS und Polypropylen ähneln.
Ein hervorzuhebender Vorteil dieser Technologien ist die außergewöhnliche Oberflächenqualität mit Rauheitswerten von bis zu Ra 1,5 μm direkt nach dem Druck. Dies reduziert den Nachbearbeitungsaufwand erheblich und macht die Verfahren besonders für sichtbare Komponenten und Designprototypen attraktiv. Die neueste Generation von PolyJet-Systemen bietet zudem die Möglichkeit, transparente Integration von digitalen Farb- und Materialbibliotheken, die auf realen physikalischen Eigenschaften basieren. Diese realistische Vorschau ermöglicht eine präzise Validierung von Design und Funktion, bevor die eigentliche Produktion beginnt.
Materialinnovationen für industriellen 3D-Druck
Die rasante Entwicklung des industriellen 3D-Drucks wird maßgeblich durch bahnbrechende Materialinnovationen vorangetrieben. Während die ersten additiven Fertigungssysteme auf wenige Standardkunststoffe beschränkt waren, umfasst das heutige Materialspektrum Hunderte spezialisierter Werkstoffe – von Hochleistungskunststoffen über Metalle und Verbundwerkstoffe bis hin zu biokompatiblen Materialien. Diese Vielfalt ermöglicht den Einsatz von 3D-Druck in nahezu allen industriellen Anwendungsbereichen.
Die Materialforschung für additive Fertigung konzentriert sich zunehmend auf die Entwicklung von Werkstoffen mit maßgeschneiderten Eigenschaften für spezifische Anwendungen. Deutsche Materialforschungsinstitute wie das Fraunhofer IFAM oder das Bayerische Laserzentrum spielen dabei eine internationale Vorreiterrolle. Allein in den letzten drei Jahren wurden über 200 neue industrielle 3D-Druckmaterialien mit optimierten Eigenschaften für Hitzebeständigkeit, chemische Resistenz, mechanische Belastbarkeit oder elektrische Leitfähigkeit eingeführt.
Ein zentraler Aspekt bei der Materialentwicklung ist die Prozessierbarkeit – der Werkstoff muss nicht nur die gewünschten Endeigenschaften aufweisen, sondern auch zuverlässig und reproduzierbar verarbeitbar sein. Die Qualifikation neuer Materialien für die industrielle Fertigung erfordert umfangreiche Tests und Validierungen, um konstante Materialeigenschaften über verschiedene Chargen und Produktionsläufe hinweg zu gewährleisten. Diese Standardisierung ist essenziell für die Akzeptanz in regulierten Industrien wie Medizintechnik oder Luftfahrt.
Hochleistungskunststoffe wie PEEK und ULTEM für Funktionsbauteile
Die Entwicklung von Hochleistungskunststoffen für den 3D-Druck hat völlig neue Anwendungsfelder erschlossen, in denen bisher nur Metalle eingesetzt werden konnten. Materialien wie Polyetheretherketon (PEEK) und ULTEM™ (Polyetherimid) bieten außergewöhnliche Temperaturbeständigkeit bis zu 260°C, hohe chemische Resistenz und bemerkenswerte mechanische Eigenschaften. Diese thermoplastischen Hochleistungspolymere ermöglichen den Druck von funktionalen Komponenten für anspruchsvolle Umgebungen wie Motorräume, Chemikalienführende Systeme oder medizinische Implantate.
In Deutschland nutzen Unternehmen wie Evonik und Ensinger ihr langjähriges Polymer-Know-how, um speziell für den 3D-Druck optimierte Versionen dieser Hochleistungsmaterialien zu entwickeln. Die Herausforderung liegt dabei in der präzisen Anpassung der rheologischen Eigenschaften, um sowohl gute Druckbarkeit als auch optimale mechanische Kennwerte zu erreichen. Bei PEEK-basierten 3D-Druckmaterialien konnten mittlerweile Zugfestigkeiten von über 100 MPa realisiert werden, was mit spritzgegossenen Teilen vergleichbar ist.
Besonders bemerkenswert ist die Entwicklung von kohlefaserverstärkten Varianten dieser Hochleistungspolymere, die Steifigkeiten im Bereich von Aluminium erreichen, bei deutlich geringerem Gewicht. Siemens nutzt beispielsweise CF-verstärktes PEEK für Robotergreifer in der Automatisierung, die bei einem Drittel des Gewichts konventioneller Metallgreifer die gleiche Last tragen können. Diese Gewichtsreduktion ermöglicht schnellere Beschleunigungs- und Bremsvorgänge, was die Produktivität der Anlagen um bis zu 23% steigert.
Metallpulver für Aerospace und Medizintechnik
Die Entwicklung spezialisierter Metallpulver hat die additive Fertigung für hochbelastete Komponenten in der Luft- und Raumfahrt sowie Medizintechnik revolutioniert. Anders als bei herkömmlichen Metallverarbeitungsverfahren erfordert der 3D-Druck sphärische Partikel mit präzise definierter Größenverteilung, Fließeigenschaften und chemischer Zusammensetzung. Führende Metallpulverhersteller wie Heraeus, TLS Technik oder H.C. Starck haben ihre Produktionsprozesse speziell für die Anforderungen des additiven Manufacturing optimiert.
Titanlegierungen wie Ti6Al4V dominieren im medizinischen Bereich aufgrund ihrer Biokompatibilität und exzellenten mechanischen Eigenschaften. Deutsche Implantathersteller wie Emerging Implant Technologies nutzen die Designfreiheit des 3D-Drucks, um Implantate mit trabekulären Strukturen zu erzeugen, die das Einwachsen von Knochengewebe fördern. Klinische Studien zeigen, dass diese additiv gefertigten Implantate eine bis zu 62% bessere Osseointegration erreichen als konventionell hergestellte Produkte.
Für Hochtemperaturanwendungen in der Luft- und Raumfahrt haben sich Nickelbasislegierungen wie Inconel 718 und 625 als Standardwerkstoffe etabliert. MTU Aero Engines verwendet diese Materialien für Turbinenschaufeln und Brennkammerkomponenten, die bei Temperaturen über 800°C betrieben werden. Die geometrische Freiheit des 3D-Drucks ermöglicht dabei die Integration komplexer innenliegender Kühlkanäle, die mit konventionellen Verfahren nicht herstellbar wären. Diese optimierte Kühlung erhöht die Lebensdauer der Komponenten um 40% bei gleichzeitiger Steigerung der thermischen Effizienz.
Verbundwerkstoffe und Faserverstärkung im 3D-Druck
Ein besonders dynamisches Entwicklungsfeld sind faserverstärkte Verbundwerkstoffe für den 3D-Druck, die die mechanischen Eigenschaften gedruckter Teile drastisch verbessern. Hier unterscheidet man zwischen kurzfaserverstärkten Filamenten, bei denen Fasern mit Längen von 0,1-0,5 mm homogen im Polymer verteilt sind, und kontinuierlich faserverstärkten Systemen, bei denen ungebrochene Faserstränge während des Druckprozesses in die Polymermatrix eingebettet werden.
Deutsche Materialspezialisten wie BASF, Covestro und LEHVOSS haben spezielle kurzfaserverstärkte Filamente entwickelt, die 20-40% Kohlenstoff-, Glas- oder Aramidfasern enthalten. Diese Materialien bieten eine isotrope Verstärkung mit Steifigkeitssteigerungen von 200-300% gegenüber unverstärkten Polymeren. Besonders im Werkzeugbau und bei Vorrichtungen für die Produktion haben sich diese Materialien bewährt, da sie deutlich kostengünstiger als metallische Alternativen sind, bei vergleichbarer Verschleißfestigkeit.
Revolutionär sind jedoch die kontinuierlichen Faserverstärkungssysteme, wie sie von Unternehmen wie Markforged oder Anisoprint angeboten werden. Bei diesen Systemen wird ein endloser Faserstrang parallel zum Thermoplast-Filament abgelegt, was zu Bauteilen mit außergewöhnlichen mechanischen Eigenschaften führt. Die spezifische Festigkeit (Festigkeit im Verhältnis zur Dichte) solcher Komponenten übertrifft teilweise sogar Aluminium und Stahl. EDAG Engineering setzt diese Technologie für strukturelle Komponenten im Automobilleichtbau ein und konnte Gewichtseinsparungen von bis zu 42% bei gleicher Leistungsfähigkeit nachweisen.
Biokompatible Materialien für medizinische Anwendungen
Der Medizinbereich profitiert besonders von der Entwicklung biokompatible Materialien für den 3D-Druck, die eine patientenspezifische Fertigung von Implantaten, Prothesen und medizinischen Hilfsmitteln ermöglichen. Diese Materialien müssen nicht nur exzellente mechanische Eigenschaften aufweisen, sondern auch strengste regulatorische Anforderungen hinsichtlich Reinheit, Sterilisierbarkeit und Langzeitverträglichkeit erfüllen.
Für permanente Implantate dominieren 3D-druckbare Titan- und Cobalt-Chrom-Legierungen, die eine hervorragende Osseointegration bieten. Unternehmen wie Fraunhofer IWU und EOS haben gemeinsam Prozessparameter entwickelt, die eine optimale Porosität für das Knochenwachstum ermöglichen, während gleichzeitig ausreichende mechanische Festigkeit gewährleistet wird. Diese porösen Strukturen mit Porositäten zwischen 30% und 80% ahmen die natürliche Knochenstruktur nach und fördern die Vaskularisierung, was die Heilungszeit nach Implantationen um bis zu 35% verkürzen kann.
Ein besonders innovatives Feld ist die Entwicklung resorbierbarer Materialien wie Polylactid (PLA) und Polycaprolacton (PCL), die sich im Körper nach einer definierten Zeit auflösen. Die TU München und das Universitätsklinikum Würzburg arbeiten an maßgeschneiderten bioresorbierbaren Implantaten, die nach der Heilung keine Zweitoperation zur Entfernung erfordern. Die Herausforderung liegt hier in der präzisen Kontrolle der Degradationsrate, die an die Heilungsgeschwindigkeit des jeweiligen Gewebes angepasst werden muss. Erste klinische Anwendungen zeigen vielversprechende Ergebnisse bei Knochendefekten im Gesichtsbereich.
Fertigungsintegration und Produktionsoptimierung durch 3D-Druck
Die wahre Revolution des industriellen 3D-Drucks liegt nicht allein in der Technologie selbst, sondern in der tiefgreifenden Transformation bestehender Fertigungsparadigmen. Durch die nahtlose Integration additiver Fertigungsverfahren in konventionelle Produktionsprozesse entstehen hybride Fertigungskonzepte, die die jeweiligen Stärken beider Ansätze kombinieren. Diese Integration erfordert jedoch ein fundamentales Umdenken in der Produktionsplanung, Bauteilkonstruktion und Lieferkettengestaltung.
Deutsche Industrieunternehmen investieren erheblich in die Entwicklung durchgängiger digitaler Prozessketten, die vom Produktdesign über die Fertigung bis zur Qualitätssicherung reichen. Siemens hat mit seiner Digital Enterprise Suite eine Plattform geschaffen, die die spezifischen Anforderungen additiver Fertigung nahtlos in bestehende PLM- und ERP-Systeme integriert. Diese digitale Durchgängigkeit reduziert nicht nur Fehlerquellen, sondern ermöglicht auch eine erheblich beschleunigte Produktentwicklung durch parallele statt sequenzielle Prozesse.
Ein wesentlicher Treiber für die Produktionsoptimierung durch 3D-Druck ist die datengetriebene Prozesssteuerung und -überwachung. Moderne Fertigungssysteme erfassen kontinuierlich Prozessdaten mittels integrierter Sensoren und Kameras, die von KI-Algorithmen in Echtzeit analysiert werden. Diese Systeme ermöglichen eine prädiktive Qualitätssicherung, bei der Abweichungen bereits während des Bauprozesses erkannt und korrigiert werden können, noch bevor das Bauteil fertiggestellt ist.
Dezentralisierung der Produktionsketten mit lokalen Fertigungszellen
Die additive Fertigung ermöglicht eine grundlegende Neugestaltung von Produktionsketten durch die Etablierung dezentraler Fertigungszellen in unmittelbarer Kundennähe. Im Gegensatz zu konventionellen Fertigungsmethoden, die oft große zentralisierte Produktionsanlagen erfordern, können 3D-Drucksysteme als flexible Fertigungszellen konfiguriert werden, die genau dort platziert werden, wo der Bedarf entsteht. Deutsche Industrieunternehmen wie Bosch und Continental haben bereits begonnen, ihre globalen Lieferketten durch strategisch positionierte 3D-Druckzentren zu ergänzen.
Besonders zukunftsweisend ist das Konzept der "vernetzten Fertigung", bei dem global verteilte 3D-Druckzellen über eine zentrale digitale Plattform koordiniert werden. Sobald ein Produktionsbedarf entsteht, wird automatisch die nächstgelegene Fertigungszelle mit freier Kapazität identifiziert und mit der Produktion beauftragt. Siemens hat mit seiner Spare Parts 4.0-Initiative bereits ein solches System implementiert, das die Lieferzeit für kritische Ersatzteile von durchschnittlich 20 Tagen auf weniger als 48 Stunden reduziert hat.
Die wirtschaftlichen Vorteile dieser Dezentralisierung sind beträchtlich: Transportwege verkürzen sich um durchschnittlich 75%, Zölle und Importgebühren entfallen, und die CO2-Bilanz verbessert sich signifikant. Ein weiterer Vorteil ist die erhöhte Versorgungssicherheit, da lokale Produktionskapazitäten weniger anfällig für globale Lieferkettenunterbrechungen sind – ein Aspekt, dessen Bedeutung durch die Erfahrungen der COVID-19-Pandemie deutlich unterstrichen wurde.
On-Demand-Fertigung und Just-in-Time-Produktion von Ersatzteilen
Die On-Demand-Fertigung durch 3D-Druck revolutioniert die traditionelle Ersatzteillogistik. Statt große Lagerbestände vorzuhalten, können Unternehmen Komponenten bei Bedarf vor Ort produzieren. Diese Just-in-Time-Produktion reduziert nicht nur Lagerkosten, sondern verkürzt auch die Lieferzeiten drastisch. Daimler Trucks beispielsweise hat durch die Integration von 3D-Drucksystemen in seine Ersatzteilstrategie die Verfügbarkeit seltener Komponenten von mehreren Wochen auf wenige Tage reduziert.
Ein besonders innovativer Ansatz ist die digitale Ersatzteillagerung, bei der nur die CAD-Daten der Komponenten gespeichert werden. Diese können bei Bedarf an jeden beliebigen Produktionsstandort übertragen und dort gefertigt werden. Volkswagen hat mit diesem Konzept sein physisches Ersatzteillager für Oldtimer-Komponenten um 50% reduziert und gleichzeitig die Verfügbarkeit erhöht.
Reduzierung von Montagekomponenten durch komplexe Druckgeometrien
Die Designfreiheit des 3D-Drucks ermöglicht die Integration mehrerer Einzelteile in eine einzige komplexe Komponente. Diese Konsolidierung reduziert nicht nur die Anzahl der Montageschritte, sondern verbessert auch die Zuverlässigkeit durch weniger Verbindungsstellen. Thyssenkrupp hat durch die Neugestaltung einer Hydraulikkomponente die ursprünglich 18 Einzelteile auf ein einziges 3D-gedrucktes Bauteil reduziert, was die Montagezeit um 75% verkürzte.
Topologieoptimierung und bionische Konstruktionsprinzipien
Die Topologieoptimierung hat durch den 3D-Druck eine völlig neue Dimension erreicht. Computergestützte Algorithmen analysieren Lastfälle und Randbedingungen, um Material nur dort einzusetzen, wo es statisch erforderlich ist. Dies führt zu bionisch inspirierten Strukturen, die das bestmögliche Verhältnis von Festigkeit zu Gewicht bieten. Namhafte Unternehmen wie Airbus und BMW nutzen diese Methode, um bis zu 50% Gewichtseinsparung bei gleichbleibender oder sogar verbesserter Bauteilperformance zu erzielen.
Besonders interessant ist die Kombination aus Topologieoptimierung und bionischen Designprinzipien. Die Natur hat über Millionen von Jahren hocheffiziente Strukturen entwickelt, die als Vorbild für technische Konstruktionen dienen. Moderne CAD-Software wie Altair Inspire oder Autodesk Fusion 360 integriert diese biologisch inspirierten Konstruktionsprinzipien direkt in den Optimierungsprozess. Das Ergebnis sind organisch anmutende Strukturen, die konventionell nicht herstellbar wären, sich aber perfekt für den 3D-Druck eignen.
Konkrete Anwendungsbeispiele aus der deutschen Industrie
Der industrielle 3D-Druck hat sich in Deutschland bereits in vielen Branchen fest etabliert. Von der Automobilindustrie über den Maschinenbau bis zur Medizintechnik nutzen führende Unternehmen die Technologie zur Optimierung ihrer Produktion. BMW beispielsweise fertigt jährlich über 200.000 Bauteile additiv, darunter Montagevorrichtungen, Prototypen und Kleinserienteile. Die Integration des 3D-Drucks hat hier zu einer Reduzierung der Entwicklungszeiten um bis zu 58% geführt.
Ein besonders eindrucksvolles Beispiel liefert die MTU Aero Engines in München. Das Unternehmen hat die Fertigung von Boroskop-Armaturen für Flugzeugtriebwerke komplett auf additive Fertigung umgestellt. Die neue Konstruktion reduziert das Bauteilgewicht um 35% und vereint 18 Einzelkomponenten in einem einzigen Druckteil. Die Montagezeit konnte dadurch von ursprünglich sechs Stunden auf nur noch 20 Minuten reduziert werden.
Auch mittelständische Unternehmen profitieren zunehmend von der Technologie. Der Werkzeugbauer Reyher aus Hamburg hat durch die Integration von 3D-Drucksystemen seine Durchlaufzeiten für Spezialwerkzeuge um 75% reduziert. Besonders bemerkenswert ist die Möglichkeit, konformgekühle Werkzeugeinlagen zu fertigen, die die Zykluszeiten im Spritzguss um bis zu 40% verkürzen.
Wirtschaftliche Aspekte und Zukunftsperspektiven des industriellen 3D-Drucks
Die ökonomischen Vorteile des industriellen 3D-Drucks werden zunehmend deutlich. Während die Technologie anfangs hauptsächlich für Prototypen eingesetzt wurde, rechnet sich der additive Fertigungsprozess heute auch für Kleinserien bis zu 10.000 Stück. Die Investitionskosten für Werkzeuge entfallen, die Lagerhaltung wird minimiert und die Flexibilität in der Produktion erhöht sich deutlich. Nach Berechnungen der RWTH Aachen können die Gesamtbetriebskosten in der Fertigung durch konsequente Integration von 3D-Druck um bis zu 25% reduziert werden.
Ein wichtiger Zukunftstrend ist die Automatisierung der additiven Fertigung. Robotergestützte Produktionszellen, die mehrere 3D-Drucker bedienen, Post-Processing durchführen und die Qualitätssicherung übernehmen, werden bereits bei Unternehmen wie BMW und Siemens erfolgreich eingesetzt. Diese automatisierten Fertigungsstraßen erreichen eine Verfügbarkeit von über 95% und können rund um die Uhr produzieren.
Die Marktprognosen für den industriellen 3D-Druck sind äußerst positiv. Experten erwarten bis 2028 ein jährliches Wachstum von 23% im deutschsprachigen Raum. Besonders die Bereiche Medizintechnik, Luft- und Raumfahrt sowie Automotive werden als Wachstumstreiber gesehen. Die fortschreitende Materialentwicklung, sinkende Systemkosten und verbesserte Prozessstabilität werden dazu beitragen, dass der 3D-Druck in immer mehr Anwendungsfeldern zur bevorzugten Fertigungstechnologie wird.
Der industrielle 3D-Druck steht erst am Anfang seiner Entwicklung. Die Kombination aus Digitalisierung, Automatisierung und kontinuierlicher Materialinnovation wird in den nächsten Jahren zu einer weiteren Transformation der industriellen Fertigung führen.
Eine zentrale Rolle für die Zukunft spielt die weitere Standardisierung der Prozesse und Materialien. Initiativen wie die VDI-Richtlinienreihe 3405 schaffen die notwendige Grundlage für eine breitere industrielle Akzeptanz. Gleichzeitig arbeiten Forschungseinrichtungen und Unternehmen an der Integration von Künstlicher Intelligenz zur Prozessoptimierung. Diese KI-Systeme werden künftig in der Lage sein, Bauteile automatisch für die additive Fertigung zu optimieren und Prozessparameter selbstständig anzupassen.